Steel Tank Linings – New Epoxy Liner
Steel Tank Linings Performed for a Corn Syrup Tank
In order to prepare to install new epoxy steel tank linings we needed effective dust control measures which we achieved with a 3 HP, 120/240 V, JET JCDC-3 Cyclone.
Because we were working on only a portion of the tank liner we needed to protect the existing coating using shielding and erect scaffolding for better access to the project area.
The old liner was removed using the process called for by SSPC 3 Standards. You can see the deteriorated liner, inside liner and steel wall (substrate) in the image below.
To ensure strong adhesion the old tank lining was removed down to bare steel (per SSPC SP-11 standards) on the ceiling and wall while maintaining the existing lower lining.
SSPC-SP11 Power Tool Cleaning to Bare Metal
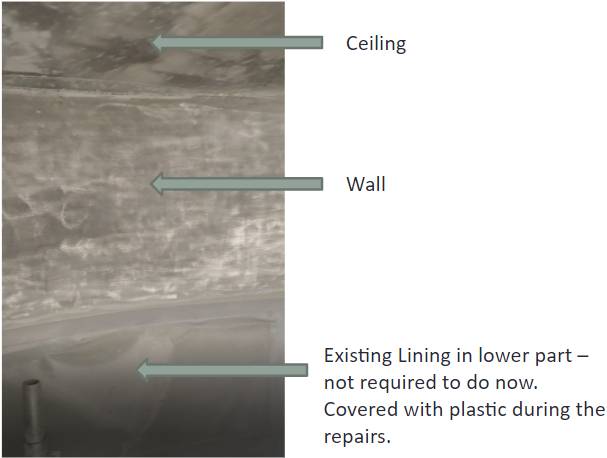
When viewed without magnification, the surface shall be free of all visible oil, grease, dirt, dust, mill scale, rust, paint, oxides, corrosion products, and other foreign matter. Slight residues of rust and paint may be left in the lower portion of pits if the original surface is pitted. The surface profile shall not be less than 1 mil
Since sand blasting was not practical for this application we used power tools including a roto-peen & bristle blaster to remove the old tank lining down to bare steel and create an anchor profile 2-5 mils per SSPC SP-11 standard.
After surface preparation surface profile tests were preformed on the tank surface to be coated. In addition environmental humidity tests were performed to ensure that the proper conditions were met for applying the Carboline Epoxy, Plasite 9133.
Wet-film thickness tests were performed during the multi-step coating process and measured 4-6 mils per coat with a total of 5 coats applied.
Computer monitored temperature control was necessary for the post-cure heating step requiring a minimum of 10 hours at 175 degrees F, we maintained the temperature for 12 hours at 175 degrees F.
Dry film thickness test was performed and measured 21-35 mils (minimum specification was 16 mils).
Electrical pin-hole detector tests were also passed showing no pin holes @ 67.5 V DC. (ASTM D5162, NACE TM0384, SP0188.)
Tank Lining Complete: All Quality Assurance Measures were Met or Exceeded
You must be logged in to post a comment.